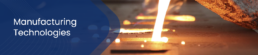
Types of Casting
The unmatched diversity of SECAN’s casting manufacturing capabilities helps us to provide a broad range of critical components to the world’s most demanding industries such as Cement, Petrochemical, Power, and Steel. At its industrial plant SECAN carries out the whole manufacturing process which includes moulding, melting,core making, shot blasting, deburring, heat treatment, and machining.
Below is an insight and about the advantages of our casting processes.
These industrial processes are underpinned by modern systems for managing production planning: ERP (Enterprise Resources Planning), MMS (Maintenance Management System) and Standardized systems for managing Quality, Environment and Safety.(ISO 9001 : 2015, ISO 14001 : 2018 and OHSAS 45001 : 2015)
Sand casting : The company avails itself of automated moulding installations for sand moulding in no bake process which is a chemical moulding, with robotics and manipulators for weightless handling, recycling of moulding sands with mechanical type. Melting are done with INDUCTOTHERM electric induction furnaces.
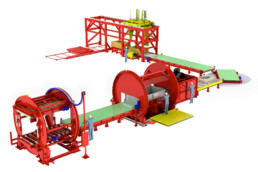
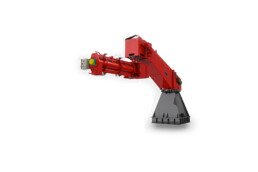
Compared to conventional sand casting, this process has better superior surface finish ,better dimensional accuracy, a higher productivity rate, and lower labour requirements. It is often used for small to medium parts that require high precision.
Investment Casting : SECAN produces complex castings with extreme precision using the “Investment Casting” method. Thanks to this versatile method our engineers have considerable freedom in the product design and choice of materials. This means that in consultation with you we can produce optimum castings that meet your exact wishes and requirements.
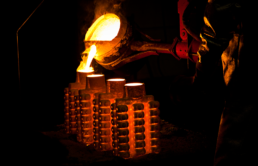
Shell Casting: Shell Casting is a metal casting process similar to sand casting, in that molten metal is poured into an expendable sand-based mould. Compared to conventional sand casting, this process has better superior surface finish ,better dimensional accuracy, a higher productivity rate, and lower labour requirements. It is often used for small to medium parts that require high precision.
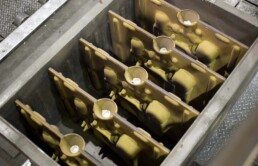
Centrifugal Casting: Centrifugal casting is a process that delivers components of high material soundness.It has also proven to be a cost-effective means of providing complex shapes with reduced machining requirements and lower manufacturing costs as compared to forgings and fabrications.
Secan produces castings weighing from few grams to 3 tonnes and ships parts globally.

Bi - Metallic castings
SECAN manufactures dual alloy castings especially where there is more wear. We insert non wearable inserts in the castings which will enhance the life of the parts serving in wear areas.
Our Markets
Our wide knowledge & experience in metallurgy with decade of experiences in process industries has helped customers & OEM for right selection of material, at competitive pricing & optimized equipment operational experiences